To manufacture prismatic and cylindrical battery cells, OEMs and battery manufacturers need a reliable partner like STIWA. We support our customers from the initial idea through product and process development to highly automated, production of millions of units – from automotive, smart mobility, energy storage, to industrial applications.
With our expertise, we ensure
efficient solutions that guarantee the highest quality and reliable results.
There are no standard solutions for the development and production of battery cell housings. Therefore, it is crucial to have a flexible partner with the expertise and competence to cover the entire process, from development to production.
An optimized cell housing design – minimizing space and complexity – plays a key role in boosting battery performance and achieving maximum energy density.
The battery housing is the central safety component that must meet the highest standards in terms of sealing, electrical conductivity, mechanical strength, and much more. It essentially consists of a battery lid / cap and a battery can – including the critical interface between these two components. High production volumes require manufacturing systems that are both flexible and highly automated to ensure constant quality and efficiency in production.
Maximum efficiency with minimum overall costs
With STIWA, you get more than just innovative solutions – you get long-term economic value. Thanks to our Total Cost of Ownership (TCO) approach, you benefit from sustainable savings. Our products and services are designed for durability and efficiency – delivering the lowest TCO through:
Requirements for battery cell housings
The requirements for battery cell housings are various and include the highest standards in terms of tightness, power transmission, mechanical stability and safety. In addition, they must be produced flexibly and efficiently in large quantities to meet the increasing market needs.
Battery cell housings must meet a wide range of demanding requirements – including the highest standards for sealing, electrical conductivity, mechanical stability, and safety. At the same time, they must be produced flexibly and in alrge quantities to meet the inreasing market demands.
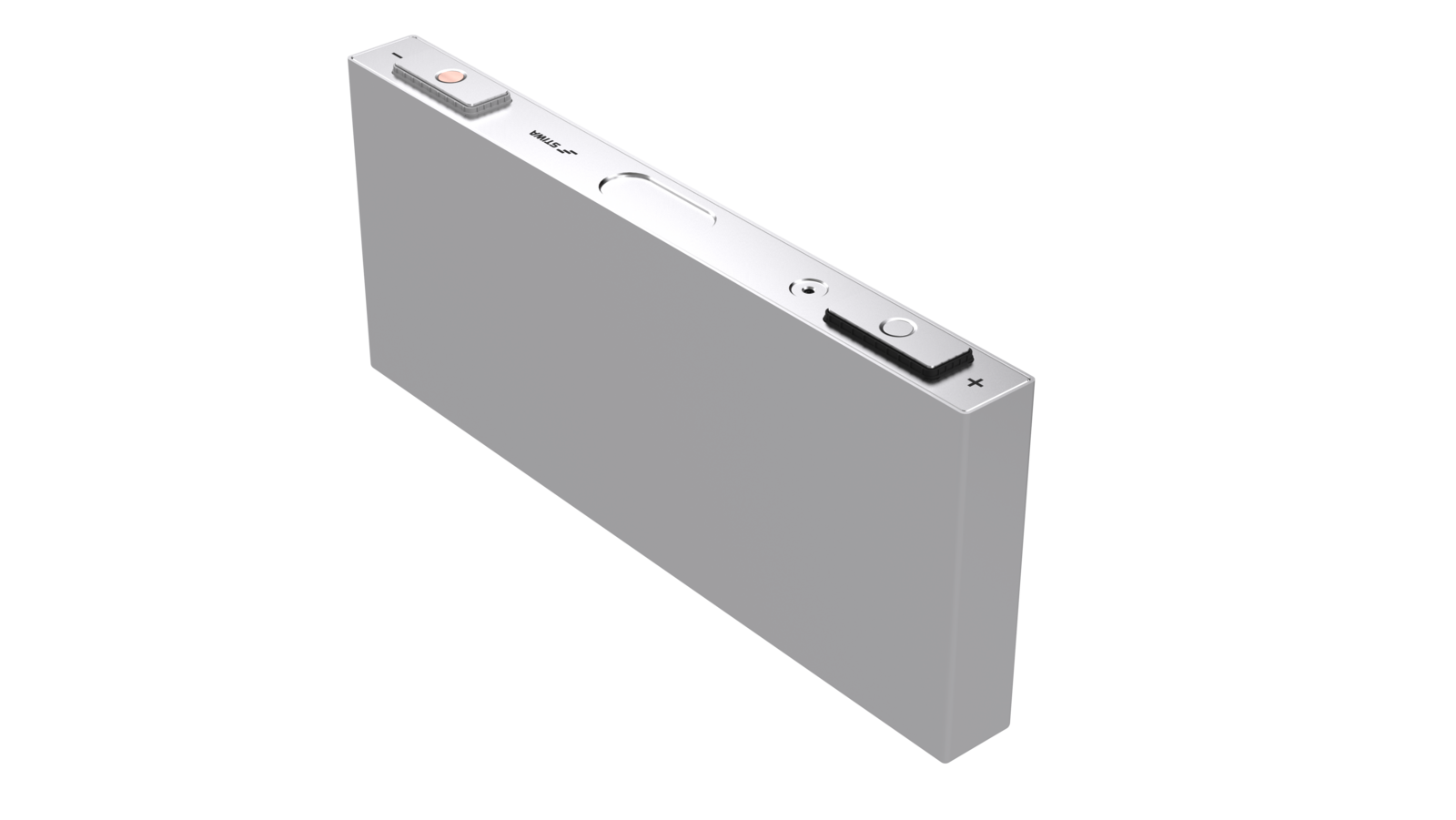
From Lab- to Gigascale
The development of battery cell housings requires the fulfillment of numerous, sometimes contradictory, functional, safety and manufacturing-specific requirements. This is a demanding task that requires a partner who competently accompanies and supports the entire process from the initial idea to the final serial production.
VENTING BEHAVIOR
Controlled release of gases and electrolyte in the event of a thermal runaway or crash
SAFETY
Compliance with standards regarding cleanliness, safety integrity, and electrical conductivity
TIGHTNESS AND ELECTROLYTE RESISTANCE
Innovative sealing concepts tailored to cell chemistry
MANUFACTURABILITY
Design-for-manufacturing, high-performance automation and 100% in-line testing
HEAT DISSIPATION
Effective heat transfer through the cell housing and the use of innovative materials
ELECTROLYTE FILLING
Optimized interface for leak-free, efficient electrolyte filling of the battery cell
JOINABILITY AND WELDABILITY
New materials require innovative technologies (e.g. aluminum/copper composite)
ISOLATION AND CONDUCTIVITY
Ensure optimum power transmission and precise design of the insulating and conductive components
MECHANICAL LOAD CAPACITY
Cells must withstand enormous mechanical loads and increase system rigidity
STIWA competencies
STIWA combines high-precision manufacturing, innovative materials, and advanced automation. From stamping and plastic parts to safety and sealing solutions, as well as complex interfaces – we develop and produce customized solutions for the highest standards.
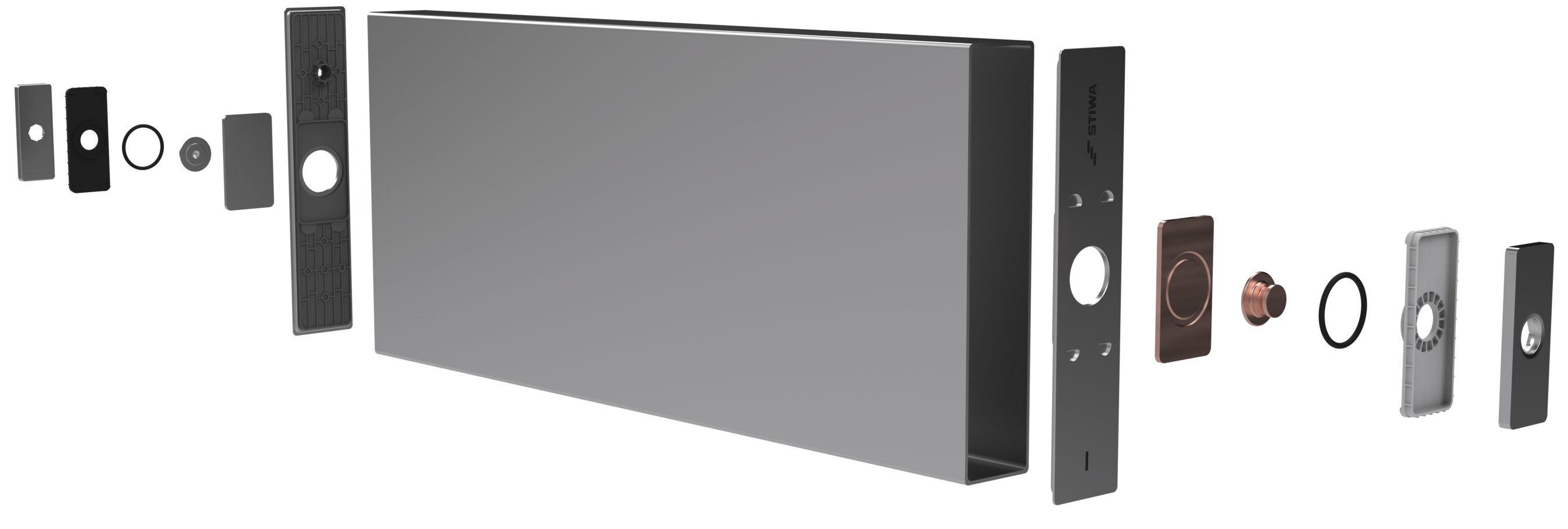
High precision bursting valves
Design and manufacture of integrated and separate bursting valves with highest tolerances and repeatability
Cap / can interface
Thanks to our in-house automation, we are familiar with complex interfaces: We think the cell housing holistically and develop both the optimal interface and the appropriate automation solution for component assembly.
High precision stamped parts
In-house, state-of-the-art punching center with its own tool construction to produce steel, aluminum and copper components according to the highest quality standards
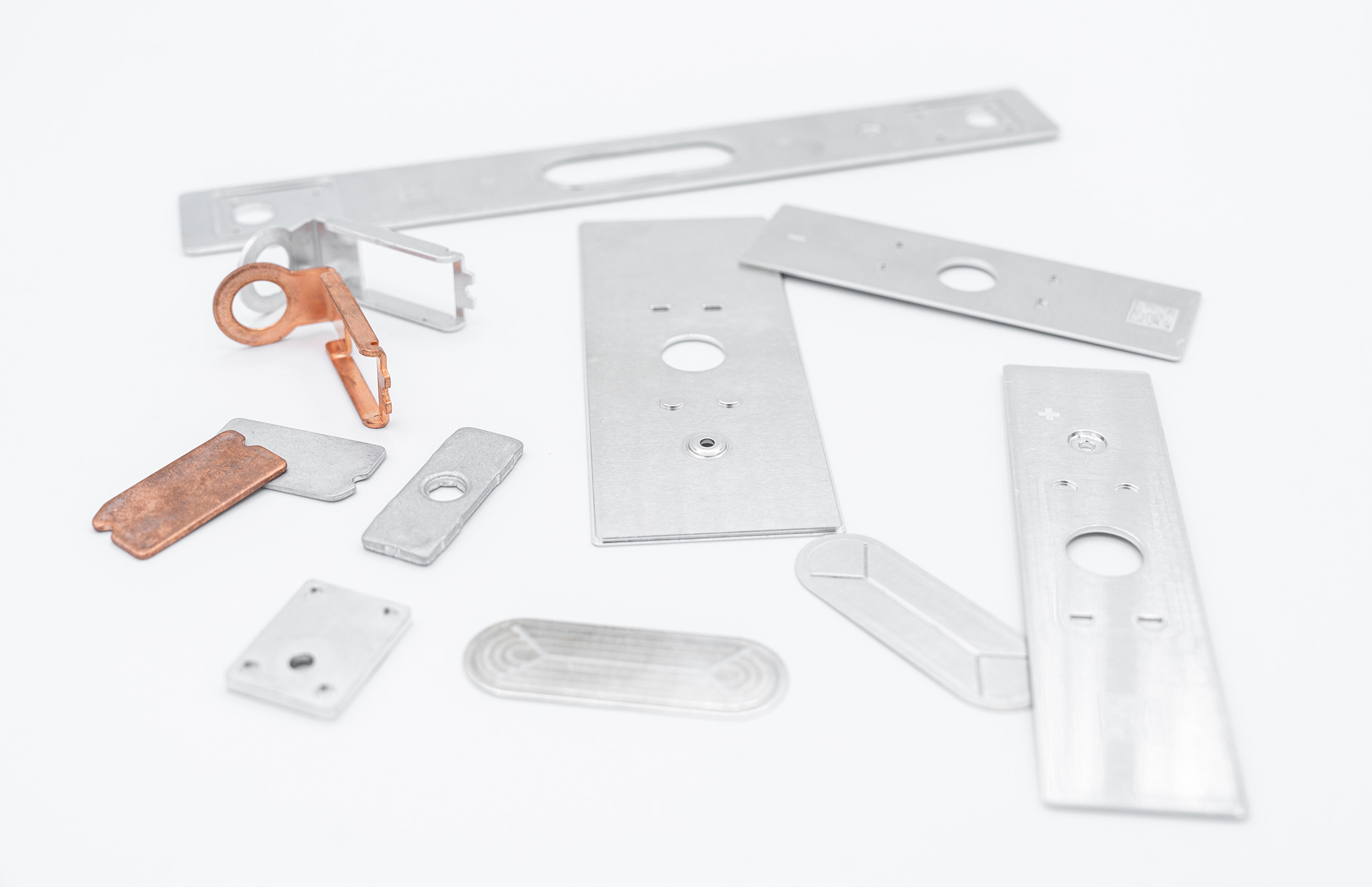
High precision stamped parts
In-house, state-of-the-art punching center with its own tool construction to produce steel, aluminum and copper components according to the highest quality standards
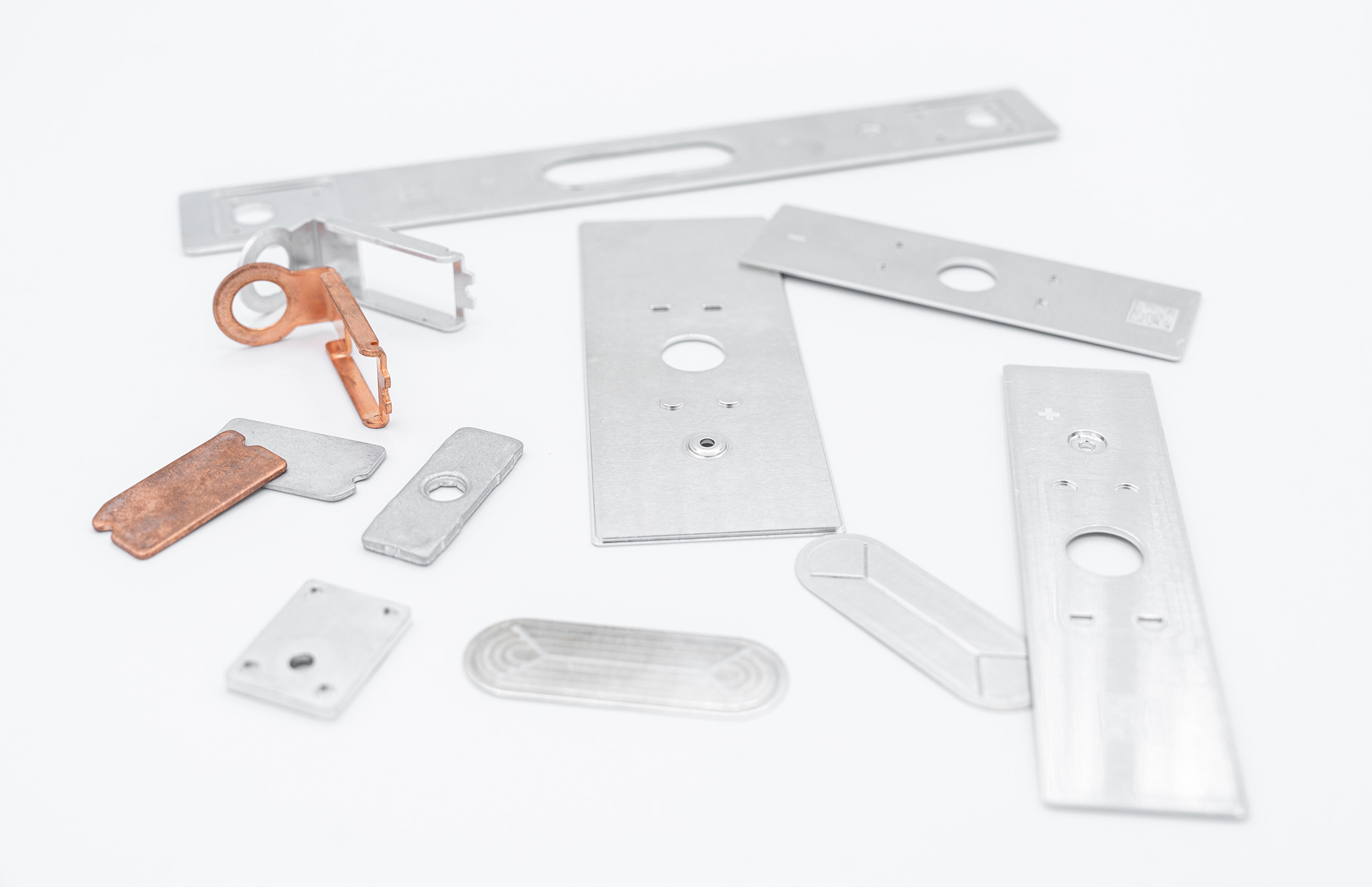
Customized sealing solutions
Working with leading seal manufacturers to develop tailor-made solutions, perfectly matched to the specifications and chemistry of the battery cell
Innovative plastic parts
In-house, state-of-the-art plastics center with its own toolmaking for injection and overmolded components – specializing in plastics for the battery industry
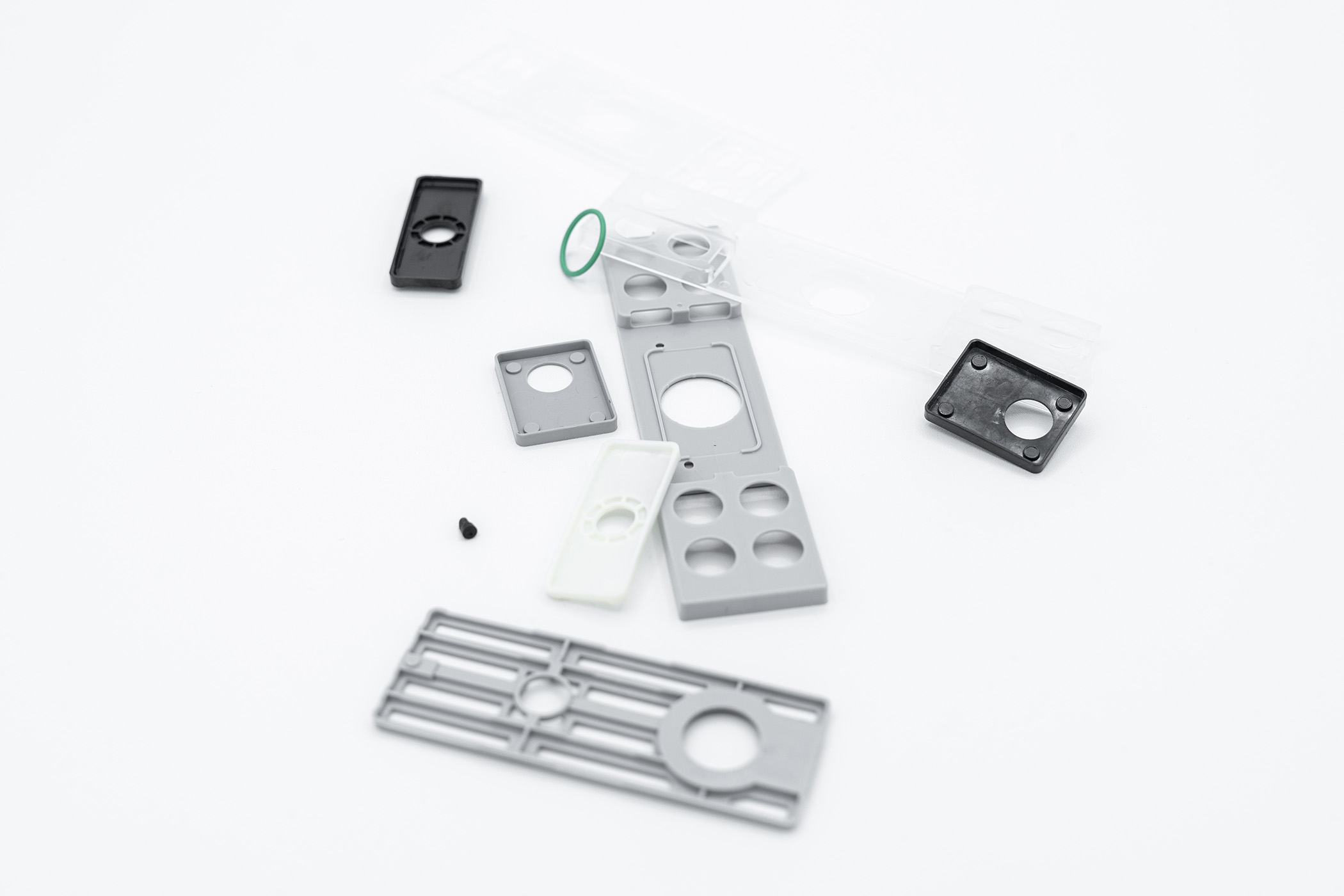
High precision stamped parts
In-house, state-of-the-art punching center with its own tool construction to produce steel, aluminum and copper components according to the highest quality standards
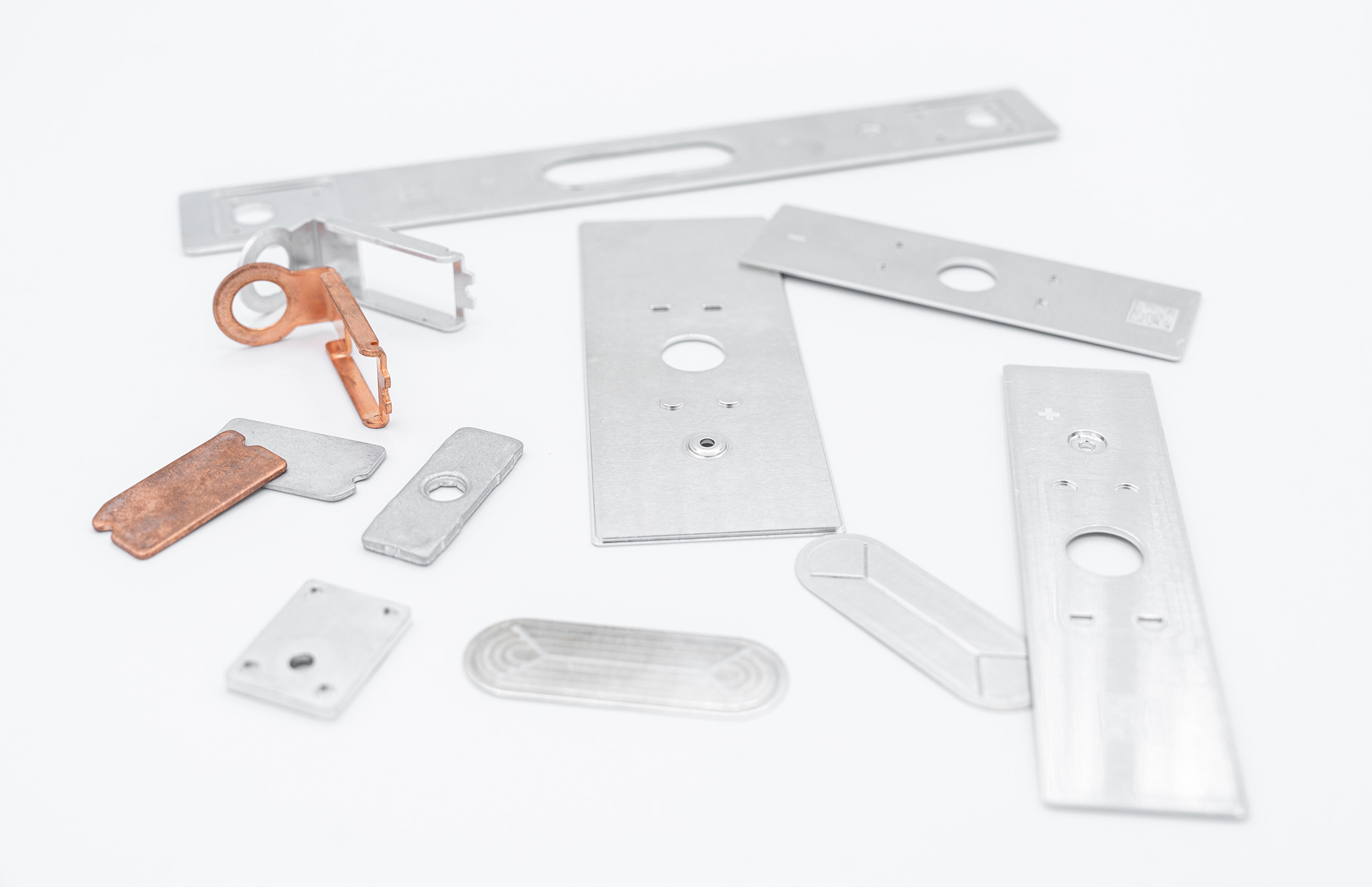
Innovative plastic parts
In-house, state-of-the-art plastics center with its own toolmaking for injection and overmolded components – specializing in plastics for the battery industry
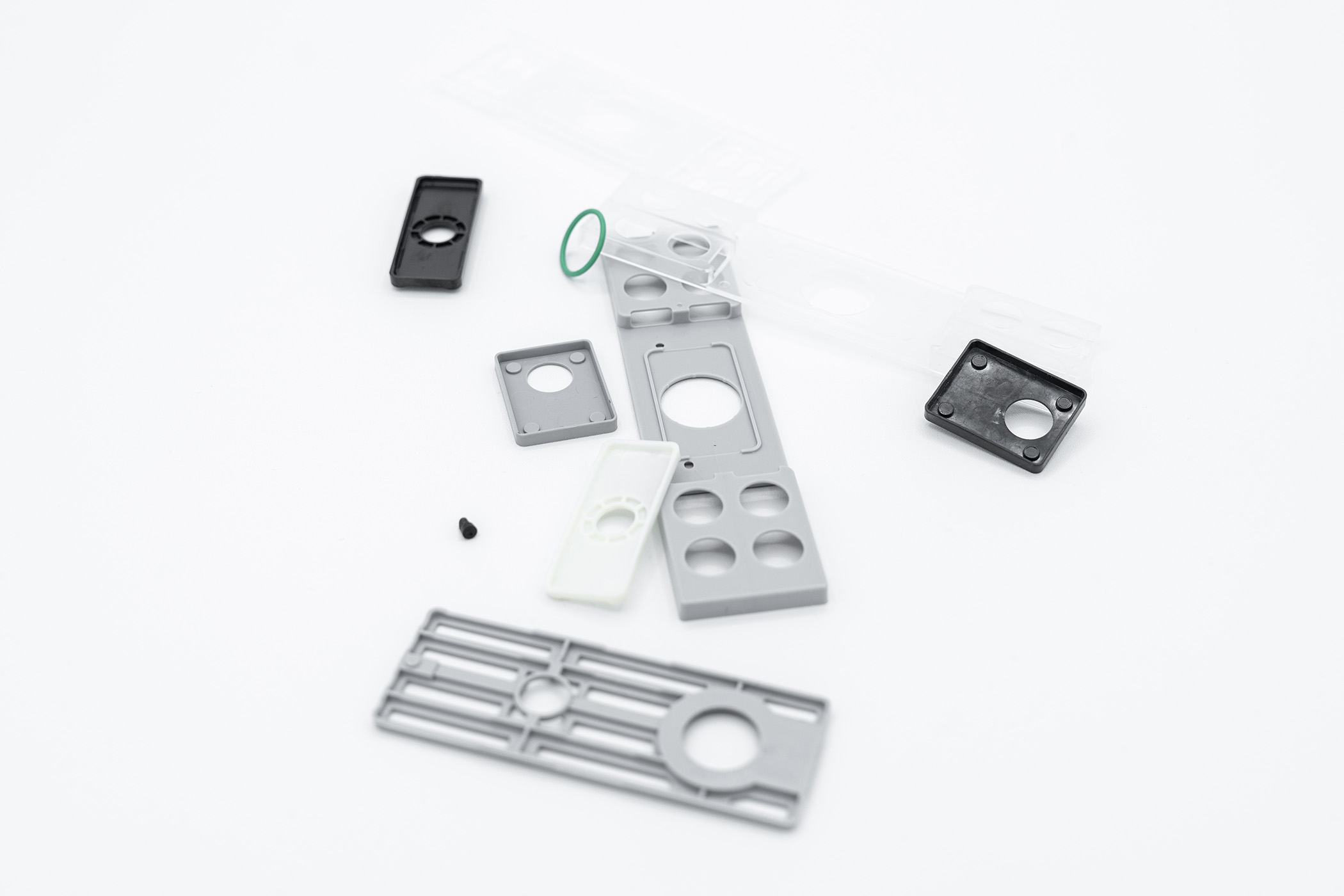
Customized sealing solutions
Working with leading seal manufacturers to develop tailor-made solutions, perfectly matched to the specifications and chemistry of the battery cell
High precision stamped parts
In-house, state-of-the-art punching center with its own tool construction to produce steel, aluminum and copper components according to the highest quality standards
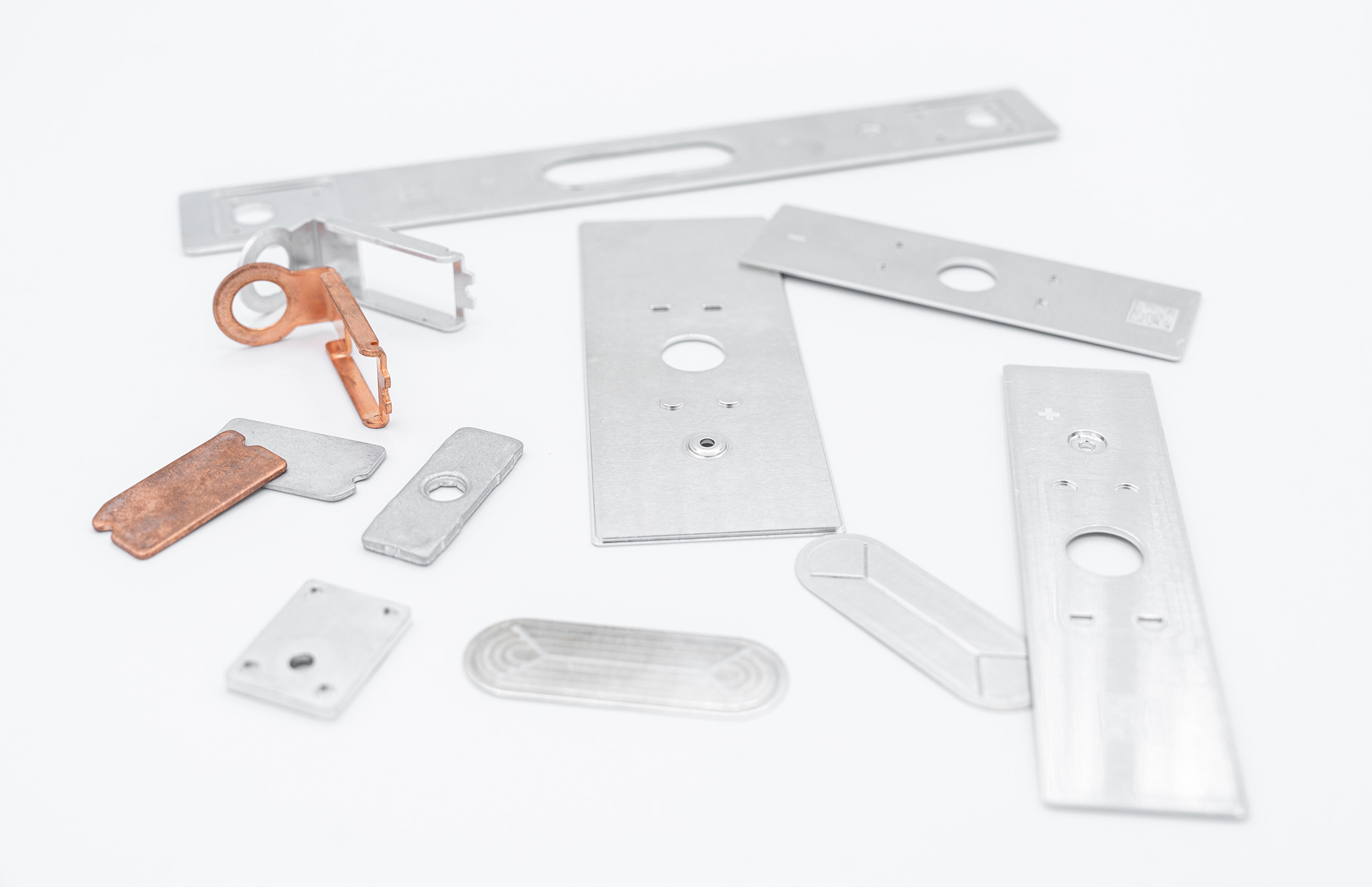
High precision stamped parts
In-house, state-of-the-art punching center with its own tool construction to produce steel, aluminum and copper components according to the highest quality standards
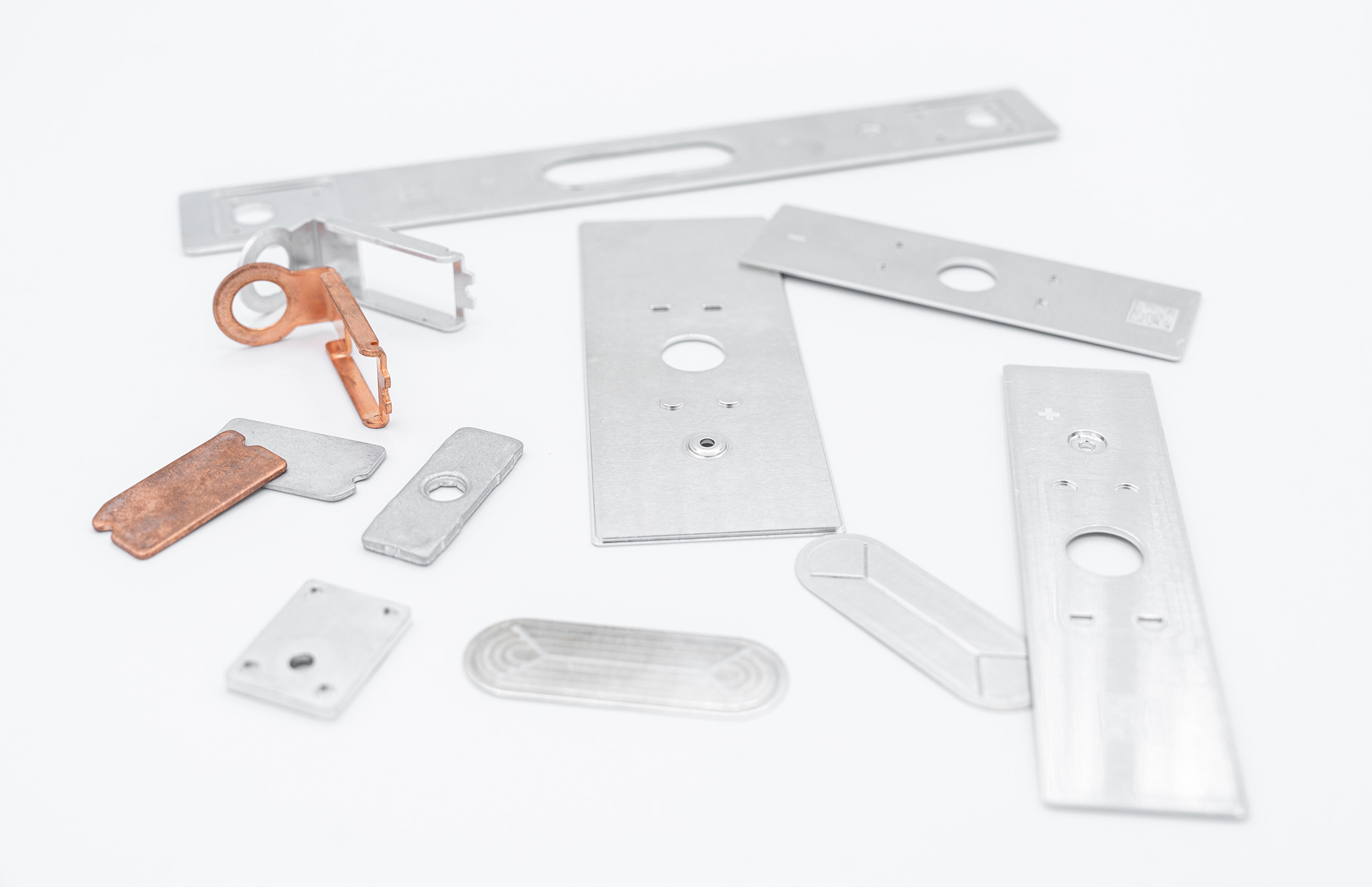
High precision stamped parts
In-house, state-of-the-art punching center with its own tool construction to produce steel, aluminum and copper components according to the highest quality standards
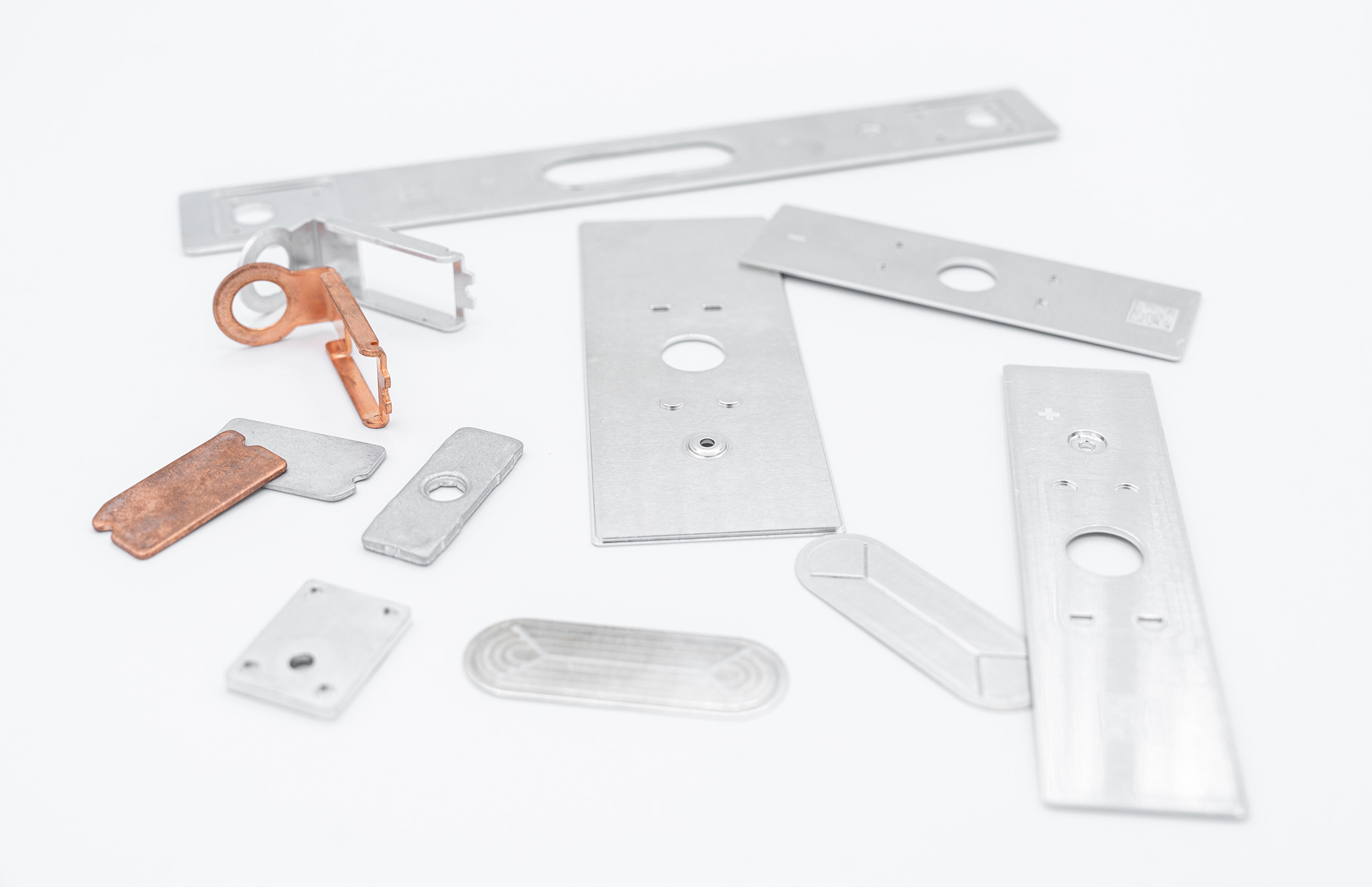
Aluminum / copper connection
We develop innovative processes and solutions for the critical aluminium-copper joints, always with the aim of reducing costs and installation space. At the same time, we promote sustainability by using less raw material.
•) For more details, click on the markers
What sets us apart -
a global partner network across the entire value chain
Research & Development
We collaborate closely with leading research institutes in battery technology to continuously integrate the latest advancements into our products and processes.
Suppliers
Sustainability and cost are key drivers of our supply chain strategy. We focus on "local for local" and sustainable materials to make the value chain more efficient and sustainable.
Partners
Thanks to close partnerships with battery cell can, sealing, and electrolyte manufacturers, we offer customized solutions from a single source to achieve best possible outcomes.
Customers
Long-term customer relationships and development partnerships enable continuous feedback, allowing us to consistently deliver innovative, market-driven solutions.
STIWAs vertical integration
From the initial idea to series production: Using state-of-the-art development, in-house prototype manufacturing, and highly automated production, we deliver precise, efficient, and future-proof solutions – all from a single source.
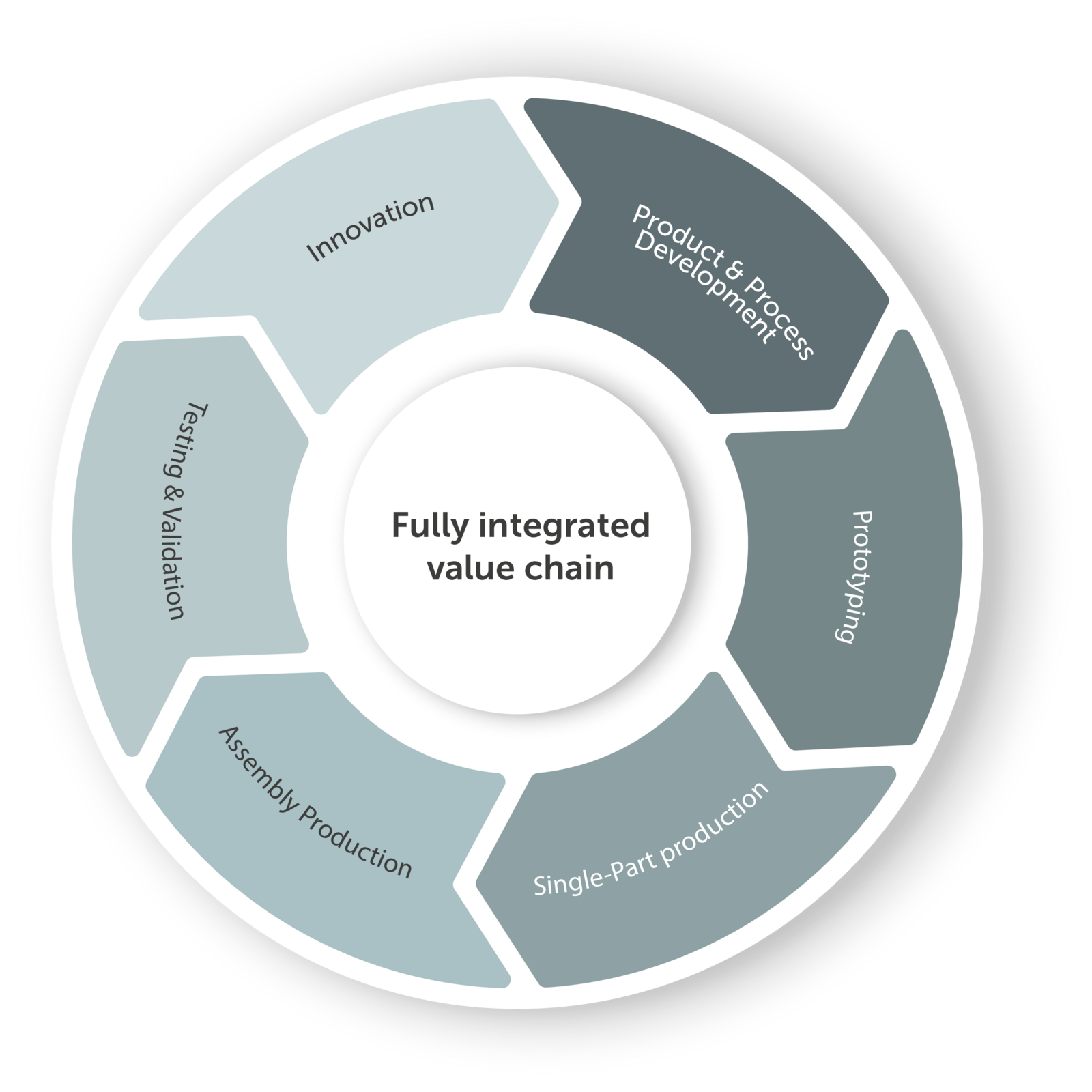
Our development team of over 50 experts covers all aspects of product and process development – from mechanical to mechatronic engineering. By combining state-of-the-art analysis methods with practical testing capabilities, we ensure the highest efficiency and innovative solutions.
Within our state-of-the-art prototyping environment, including a cleanroom facility, we offer comprehensive technologies to support innovative products from development through production to extensive testing. Our testing capabilities cover mechanical stress tests, leak and burst tests, as well as electrical voltage and resistance measurements. This ensures the foundation for reliable, high-quality series products — with prototype volumes of up to several thousand units per week.
The production of individual parts – from stamped and plastic components to precision-machined parts – is carried out directly in-house at STIWA. Our deep manufacturing expertise allows us to fully understand component interactions and respond with maximum flexibility to product optimizations and changes. This enables us to quickly and efficiently meet customer requirements and technical adjustments.
Thanks to the highly automated solutions of our sister company STIWA-Automation, we achieve the fastest cycle times and ensure the lowest total costs as well as the highest quality through 100% in-line testing.
To ensure our products meet the highest quality standards, we offer all relevant testing procedures in-house. From cleanliness analyses and material inspections to mechanical durability tests, we cover the full spectrum.
Our goal is not only to develop solutions for current requirements but also to develop innovations that give our customers a decisive competitive advantage in the dynamic market.
STIWA automation line
From the first production stage to the final assembly group, we focus on the highest quality standards, maximum flexibility and cleanliness. Our processes guarantee precision, scalability and efficiency – perfectly matched to the requirements of the battery industry.
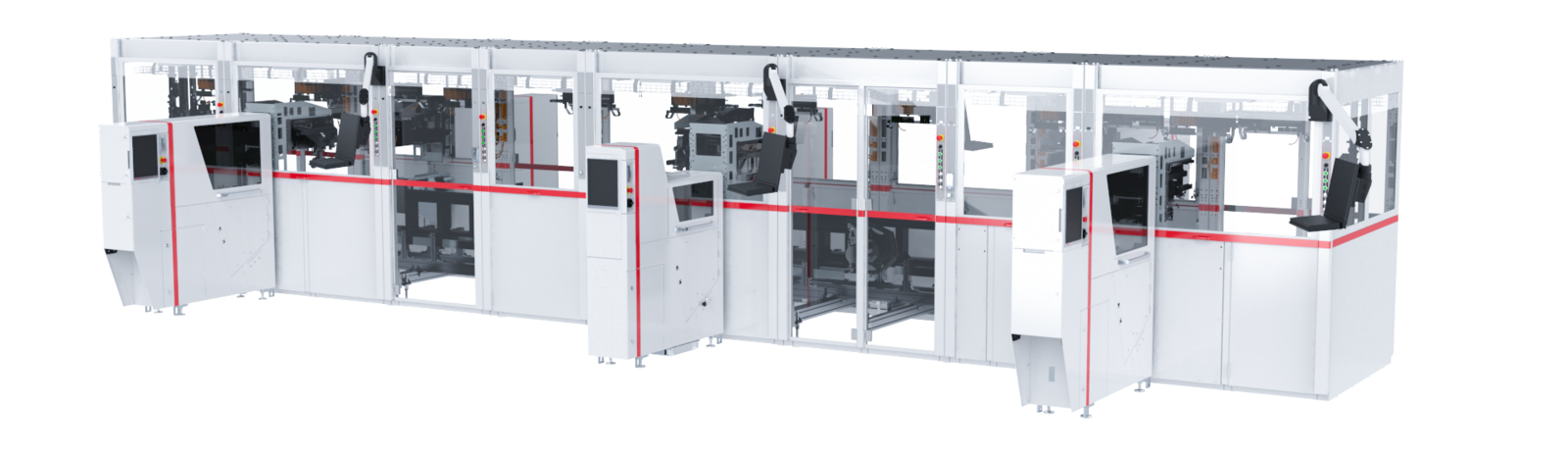
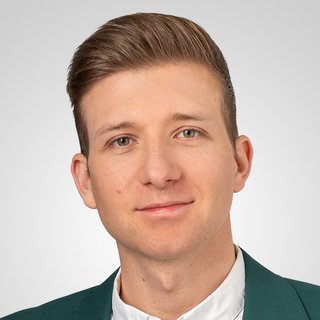
Oliver Schwarz
Business Development Battery
STIWA Advanced Products