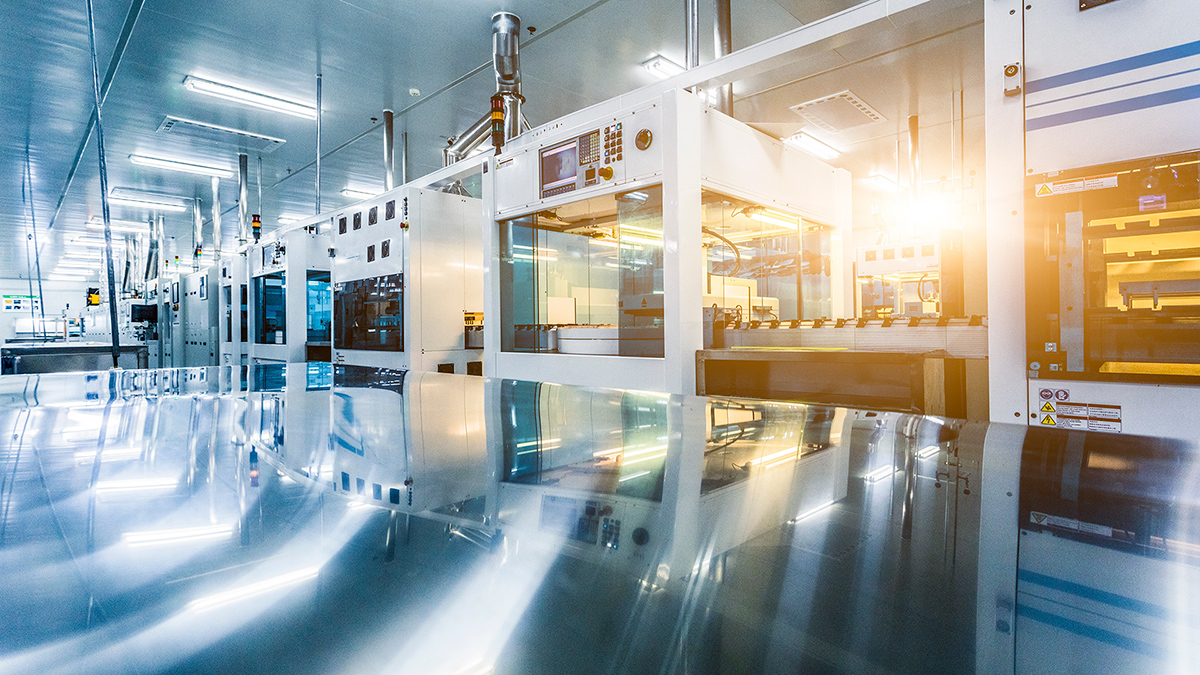
Optimize Production with Data-Driven Solutions
Achieve higher quality, more stable processes, and reduced cycle times with tailored strategies. Leveraging expertise in mechanical engineering and production, advanced data models and analysis tools enhance machine efficiency during production.
Through workshops, specialists collaborate to define requirements and implement solutions that maximize the value of your production data—from control systems to complex machine learning models—ensuring seamless integration and optimized performance across facilities.
Unlock the full potential of your operations with tailored analysis, targeted optimization, and hands-on strategies designed to increase efficiency and production quality.
We assist you
in reaching your goals:
As a production or plant manager, reducing production costs while maintaining high-quality standards is a top priority. Achieving this requires a clear view of the factors influencing your production processes and products, along with tools to quickly identify and address malfunctions. To ensure sustainable increases in plant efficiency and make informed decisions for initiatives like sourcing, rely on expert support tailored to your needs. Backed by specialists in production, mechanical engineering, and software, you can drive operational success with confidence.
As a member of management, shaping your company’s future and choosing the right partners are key responsibilities. In times of global supply chain uncertainty, transparent production site analyses and efficient launch management are essential. Gain the insights and expertise needed to drive growth with solutions tailored to your strategic goals and operational challenges—supported by a team of specialists in production, engineering, and software.
As a production planner, the right tools are essential for analyzing data, responding quickly to trends, and learning from past interrelations to implement targeted measures for future success. With actionable insights and solutions designed to support your planning needs, you can ensure efficiency and adaptability at every step of the production process—all backed by experts in production, engineering, and software
As a maintenance manager, ensuring machine availability is your primary responsibility. This requires a clear view of current machine conditions, tools to quickly identify failure causes, and insights to uncover interrelations. Reliable information is also essential for planning optimal maintenance intervals. With the right support and solutions, you can achieve these goals effectively—keeping machines running smoothly and minimizing downtime. Supported by specialists in production, mechanical engineering, and software, you’ll have the expertise needed to maintain peak performance.
As a quality manager, your role is to standardize and stabilize processes while improving quality standards. Regular collaboration with Production Management ensures progress toward these goals. To address complex problems, quick and accurate analyses are crucial, supported by consistent and comprehensive data that uncover cause-effect relationships. Achieve lasting improvements with tailored solutions and expert guidance. Supported by specialists in production, mechanical engineering, and software, you’ll have the tools and insights needed to drive production excellence.
Our Workshop-Packages
Achieve higher quality and more stable processes while reducing cycle times with STIWA Shopfloor Software. Gain full control over production with detailed technical analyses that boost performance across individual facilities and entire factories. This ensures optimized, reliable, and efficient operations—no matter where you are in the world.
To support this, workshop packages provide the opportunity to familiarize yourself with the approach and services—from the initial analysis to defining the right strategy for specific production needs.
Analysis BASIC Workshop Package
Do you need a foundational assessment to identify key improvement areas using your production data?
Initial insights into problem areas using data collection.
- Challenge:Identifying hidden inefficiencies in production.
- Solution: Data-driven assessment to reveal key improvement areas.
Steps:
- Fully automated data collection.
- Identification of key areas for improvement.
- Report with foundational insights and next steps.
Optimization PLUS Package
Are you aiming to tackle complex issues across multiple, interconnected processes to enhance efficiency?
Advanced problem-solving for complex, linked processes.
- Challenge: Optimizing complex, interconnected processes.
- Solution: Targeted strategies to streamline and enhance efficiency.
Steps:
- Assess complex, multi-step processes to pinpoint improvement areas.
- Formulate custom optimization strategies targeting interconnected systems.
- Implement targeted interventions to enhance overall efficiency.
Production EXCELLENCE Workshop Package
Are you ready for a comprehensive digitization approach to maximize production performance and strategic insights?
Comprehensive digitization strategies for improved production efficiency.
- Challenge: Struggling to generate and implement innovative improvements?
- Solution: A comprehensive roadmap for digital transformation and sustainable improvement.
Steps:
- Perform a full-scale digital analysis of production systems.
- Develop a strategic plan for digital integration and process improvements.
- Provide a roadmap with measurable steps for sustained optimization.
ADJUSTMENTS OF SAMPLING FREQUENCIES
for better usability
DATA CHECKS
for consistency checks
CONNECTION OF CONTROL
to data infrastructure with corresponding data model for efficient saving and evaluation
PROCESS MONITORING
via anomaly detection
DETECTING
of trends
CAUSE RESEARCH
via correlation analysis
CROSS-PROCESS ANALYSES
for quality assurance
MACHINE SIMULATION
with jam analyses for cycle time optimization
Workshops
Data science and analytics
As the mechanical engineer and producer, we develop the data models and analysis tools to increase the efficiency of the machine during production using data evaluation.
In the course of the workshop, we establish those requirements and solutions with our specialists that draw the maximum possible benefit from the data and, therefore, support the data value chain from the control to the complex Machine Learning model.
- Initial Data Collection and Assessment: Approx. 1 day
- Together with your experts define:
- Best application
- Ideal solution approach
- Use cases and KPIs
- Identify Improvement Areas:
- Pinpoint key opportunities.
- Together with your experts define:
- Software installation: Approx. 1 day
- Quick setup with certified hardware or direct system installation.
- Data Collection & Evaluation: Approx. maximum of 2 months
- Collect, network, and interpret data remotely or on-site (Approx. 1 day)
- Analyze and evaluate collected data together.
- Final Report & Strategic Alignment: Approx. ½ day
- Present performance based on KPIs.
- Define the next steps for optimizing production processes.
- Final report with all involved.
- Initial Data Collection and Assessment: Approx. 1 day
- Together with your experts define:
- Best application
- Ideal solution approach
- Use cases and KPIs
- Identify Improvement Areas
- Pinpoint key opportunities
- Together with your experts define:
- Software installation: Approx. 1 day
- Quick setup with certified hardware or direct system installation.
- Deep integration of the three most essential modules (stations) in your assembly system.
- On-site data check to understand machine performance and processes.
- Data Collection & Evaluation: Approx. maximum of 2 months
- Collect, network, and interpret data remotely or on-site (Approx. 1-2 days)
- Analyze and evaluate collected data together.
- Use software and apply demonstrated methods independently.
- Final Report & Strategic Alignment: Approx. ½ day
- Present performance based on KPIs.
- Concrete assistance, suggestions for improvement, and an overview of continuous software benefits.
- Define the next steps for optimizing production processes.
- Initial Data Collection and Assessment: Approx. 1 day
- Factory visit for our experts to understand your unique needs.
- Jointly define workshop objectives with your expert team.
- Software installation: Approx. 2 days
- Multi-day workshop with experts and decision-makers.
- Assess the current situation and develop a target state based on:
- Employee roles
- Software & hardware infrastructure
- Network topology
- Quantity structure of products and data, etc.
- Rollout scenarios
- Data Collection & Evaluation: Approx. maximum of 2 months
- Develop an optimal strategy to bridge the current and desired states.
- Final Report & Strategic Alignment: Approx. ½ day
- Present the developed strategy to all involved.
- Build a network of key contacts to guide implementation.
- Establish a stable foundation for your digitization journey.
- Use-Case Identification: Approx. 1 day
- STIWA Service: Identify solutions tailored to your needs.
- Customer Role: Ensure all relevant areas are informed.
- Software Installation: Approx. 1 day
- STIWA Service: Concept creation, configuration, installation, on-site data control, and commissioning.
- Customer Role: Support possible integration of STIWA modules into PLC systems and provide access for remote testing.
- Data Collection & Evaluation: Approx. maximum of 2 months
- STIWA Service: Conduct data analysis, a workshop, and develop optimization measures.
- Customer Role: Implement optimizing strategies and integration of PLC modules.
- Presentation & Next Steps: Approx. ½ day
- STIWA Service : Present results and propose holistic optimization solutions.
- Customer Role: Ensure all areas are integrated into the process.
- Understanding the Current Situation: Approx. 1 day
- STIWA’s Service: Factory visit and gather production insights.
- Customer’s Role: Inform all affected areas and provide technical data.
- Establishing the Desired State: Approx. 2 days
- STIWA’s Service: 2-day workshop to define goals and strategy.
- Customer’s Role: Ensure all relevant departments are informed and engaged.
- Developing Strategy: Approx. maximum of 2 months
- STIWA’s Service: Create a strategic roadmap with customer experts.
- Customer’s Role: Provide ongoing support and queries as needed.
- Presentation Results: Approx. ½ day
- STIWA’s Service: Present the finalized strategy and next steps.
- Customer’s Role: Ensure smooth integration across departments.
This is what
our customers say
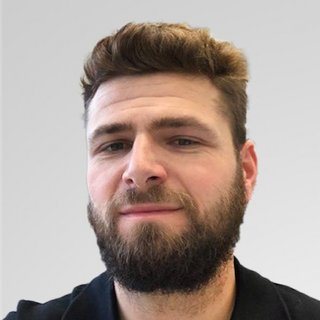
“The improved Andon Boards and the Shopfloor Monitor ensure clarity and a complete overview. It motivates you and makes it much easier to manage the day-to-day business. The OOE increases!
Benjamin Heim
Management assembly VUVG-valves Festo AG & Co. KG
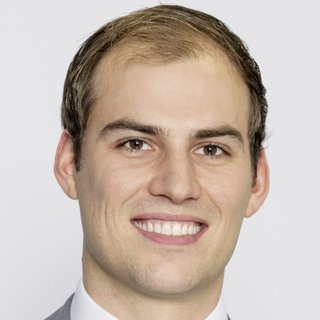
Within a few weeks, the OK output of the plant was increased by more than 10 %. The reject rate was reduced significantly. After one year, the rate of increase of OK output already stood at 40 %.
Kilian Seiler
Project manager Festo AG & Co. KG
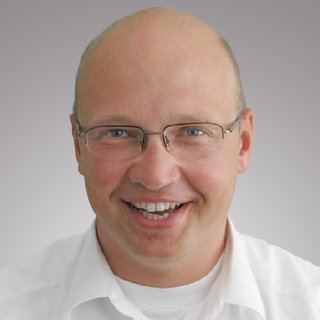
Without the AMS Analysis-CI we’d not have achieved what we have today - namely a transparent, reliable, and controlled production. By means of AMS-Analysis CI, we could reduce our ramp-up time by 30 to 40 percent!”
Peter Nieslon
Manager Industrial Engineering Valeo Wischersysteme GmbH
Global expertise, tailored to your requirements
Successful collaboration is the key to success. Working in partnership with your team, interdisciplinary experts from the fields of automation, production, and data analysis develop comprehensive strategies for collecting, analyzing, and optimizing production data throughout the entire value chain, from basic manufacturing to final assembly.
With many years of experience, STIWA's production experts support the implementation of these measures directly in your plant, delivering visible results within a short period of time.
For almost 50 years, leading global companies and hidden champions have relied on STIWA's customized software and service solutions. With worldwide support and comprehensive after-sales service, optimizations are sustainably secured and adapted to your locations worldwide to ensure long-term competitive advantages.
Worldwide support
USA
Fort Mill
Contact Person: |
CHINA
Nantong 1
Contact Person: |
GERMANY
Wilnsdorf
Contact Person: Michael Meisel CEO: |
AUSTRIA
Attnang-Puchheim 1
Contact Person: |
|
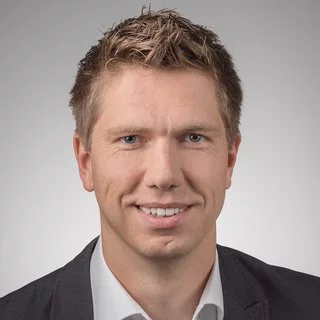
Mag. Alexander Meisinger, MSc
Head of Customer Success Management
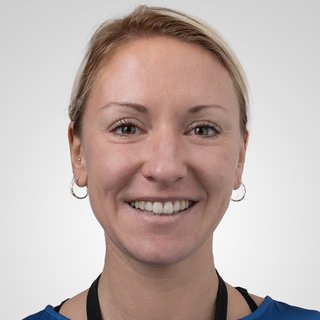
Dipl.-Ing. Dagmar Reindl, BSc
Customer Success Management