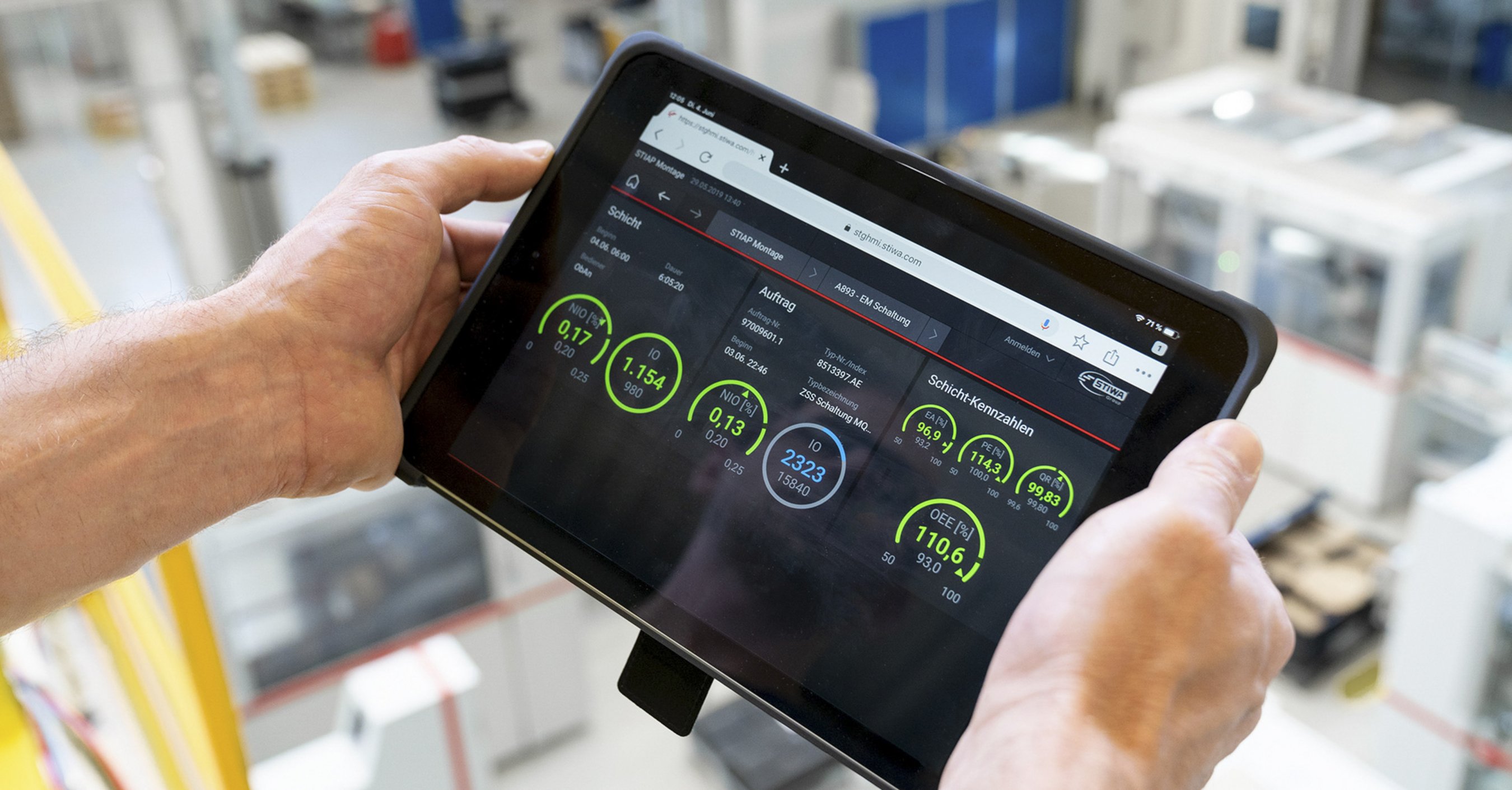
Defective feeding material that leads to increased rejects, incorrectly set screwing processes, that block the workpiece carrier for a long time and handling mistakes that entail hard module standstills: technical, mechanical or organizational problems can lead to various cycle time overruns. The STIWA shopfloor experts will make your production processes transparent and thus can increase the machine efficiency by more than 10 percent within a few weeks.
To solve complex problems of production quickly, immediate cause and effect analyses are necessary. STIWA shopfloor experts therefore assist in detecting complex connections in production, identifying problem situations like unstable production processes or low availability, fixing them and in doing so achieving a significant performance increase of production facilities. In an interdisciplinary optimization team from automation, production and analytics, the basis for a comprehensive evaluation and optimization of the production is created along with the customer. Data will be recorded and analyzed along the whole value chain, starting from basic manufacturing to pre-assembly though to final production. The process steps that are associated with the production process are measured as well, like energy, logistics or material. The results are apparent with a short time: For example, this is how in the project with Festo International the OK output of the machine was increased by more than 10% and the reject rate reduced significantly. After one year, the rate of increase of OK output already stood at 40 %.
Significantly shorter ramp-up time
There is also a lot of potential for optimization during the ramp-up phase: With the high performance, scalable and adjustable STIWA analysis tools, machine-, operation- and quality data can already be acquired during the ramp-up phase that serve as the base for optimization measures concerning performance, availability and quality. Problems and connections can be exposed “live”. Thus you can for example detect the slowest and cycle time determining production module via the cycle time analysis or the workpiece carrier that causes problems in certain assembly processes. Previous experiences confirm the high effectiveness of an increase in machine transparency during ramp-up: For example at Valeo Wischersysteme GmbH the data based monitoring of a production launch led to a reduction of the lead time by about 30 to 40 percent. Accordingly, the machine was able to produce to budget costs quicker.
The STIWA shopfloor experts realize competitive advantages on a permanent basis. That is why both world market leaders and hidden champions have relied on the know-how of STIWA Group for almost 25 years.